Time for a Checkup!
July 29, 2021
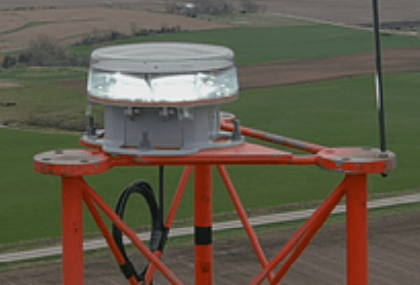
FAA Required Biennial Lens Inspection
Many tower owners with obstruction lighting systems may be unaware, or uninformed, of the facts regarding the FAA’s requirement for biennial lens inspection. Let LumenServe℠
shed some light on the mystery to ensure you are in full compliance.
The Requirement
Let’s start with the requirement which was initiated with revision 1L of the FAA circular governing tower lighting and continues to be included in the most recent circular – 1M . Below is an excerpt from the FAA’s Advisory Circular for Obstruction Lighting and Marking - AC No. 70/7460-1L Change: 1
Date: 10/8/2016 Paragraph 4.5:
Due to the effects of harsh environments, light fixture lenses should be visually inspected every 24 months, or when the light fixture fails, for ultraviolet (UV) damage, cracks, crazing, dirt buildup, etc., to ensure the certified light output has not deteriorated. (See Chapter 2 paragraph 2.4 for reporting requirements in case of failure.) Lenses that have cracks, UV damage, crazing, or excessive dirt buildup should be cleaned or replaced.
By the way, the LumenServe℠ Federal Lighting Regulations Portal
provides an easy to navigate and comprehensive link to key regulatory websites as well as the best graphical illustrations to help simplify things.
The Intent
The intent of the lens inspection requirement is clearly (pun intended) stated to “ensure the certified light output has not deteriorated.” The purpose is to make sure the system is emitting light pursuant to specifications of the manufacturer’s equipment which has been approved by the FAA, and that there is nothing wrong with the lens performance which is causing a degradation of light emission.
What to Look For
The system should be visually inspected which means a tower climb or a high-resolution drone video to each of the lighting fixtures – all beacons and sidelights. The inspection should look for “ultraviolet (UV) damage, cracks, crazing, dirt buildup, etc.” The “etc.” in this instance could include unwanted deposits on the outside of the lens (think bird poop as an example), or unwanted deposits on the inside of the lens. LumenServe℠ has seen instances where material inside a legacy lighting system, such as certain types of tape, are vaporized and then deposited on the inside of the lens. This is a result of a poor installation and must be addressed. Certain older models of lighting lenses are made of older plastics that are affected by UV rays resulting in crazing. Old glass lenses can chip. The bottom line is the inspection relies on the reasonable judgement of the inspector to determine if the lens performance is degraded in some manner and decreasing the system’s certified output. No light meter or measurement is required, just a thorough inspection and reasonable determination of the status of each lens.
How Often to Inspect
The requirement states that “light fixture lenses should be visually inspected every 24 months, or when the light fixture fails.” Failure of the fixture indicates that the fixture must be repaired and thus makes for a good opportunity to inspect the lens, otherwise the lens should be inspected every two years.
How to Document and Record Keeping
The process LumenServe℠ utilizes to document the biennial lens inspection is to photograph three photos of each lens with each photo covering at least 120 degrees arc around the periphery of the lens to ensure that the full 360 degrees of the lens has been documented. The photos are embedded in a Biennial Lens Inspection package which provides all the pertinent information including: site name, ASR, location, FAA Style, inspection notes, inspection technician information, date, etc. This documentation is held for a minimum of two years, but usually longer.
If you need any help with biennial lens inspections, or any other aspect of tower lighting, LumenServe℠ can help you analyze the costs and benefits of all your options. Also, don’t forget, as the nation’s first Tower Lighting as a Service®
company, LumenServe℠ can provide qualified customers with a lighting solution that requires no upfront costs. Let us look at your situation and see if we can give you peace of mind
regarding your tower lighting.
For more information, please contact LumenServe℠
today!
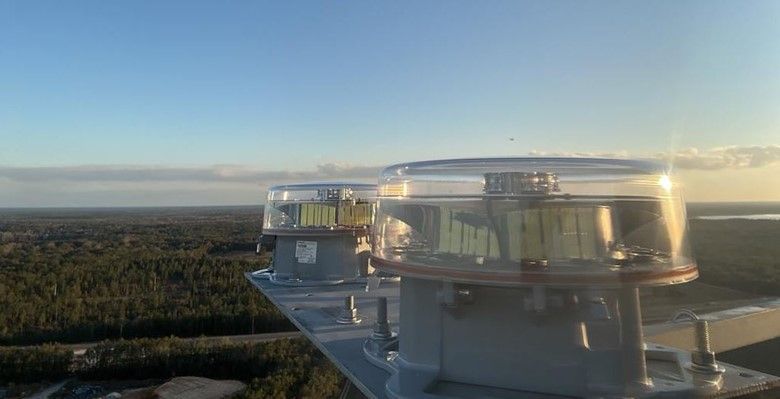
We extend our condolences to the families impacted by the recent helicopter crash in Houston’s Second Ward. While the cause is still under investigation, this tragedy is a reminder of how crucial obstruction lighting is for aviation safety. At LumenServe ℠ , we are dedicated to delivering innovative solutions that ensure your towers meet federal compliance standards, operate at peak efficiency, and ultimately protect lives. With cutting-edge technology, including Infrared (IR)-capable LED lighting systems, we help you stay ahead in safety and compliance without compromising on quality or cost.
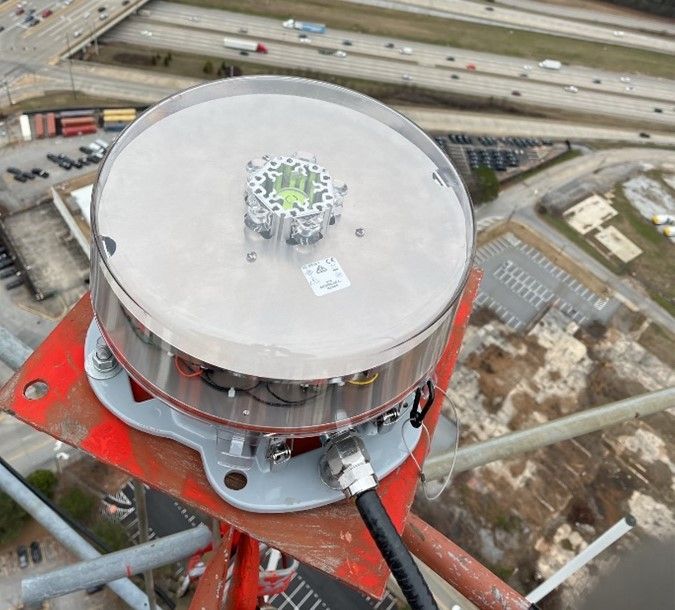
Effective as of September 11, 2020, the FAA requires Infrared Emitters (IR) for your LED obstruction lighting for newly constructed towers or circular updates. The FAA’s Advisory Circular (AC) spells out the specifications for IR and obstruction lighting equipment. The obstruction lighting rules were created in response to the Safety Risk Assessment of LEDs in Aircraft Operations with the FAA establishing IR specifications for LED based obstruction lights. Specifications are contained in Airport Engineering Brief 98 and Infrared Specifications for Aviation Obstruction Light Compatibility with Night Vision Goggles, published December 18, 2017. Military, emergency service, and other helicopter pilots are starting to use NVGs more frequently for increased safety and to amplify visible light. The illustrations below highlight the need for IR with your obstruction lighting.
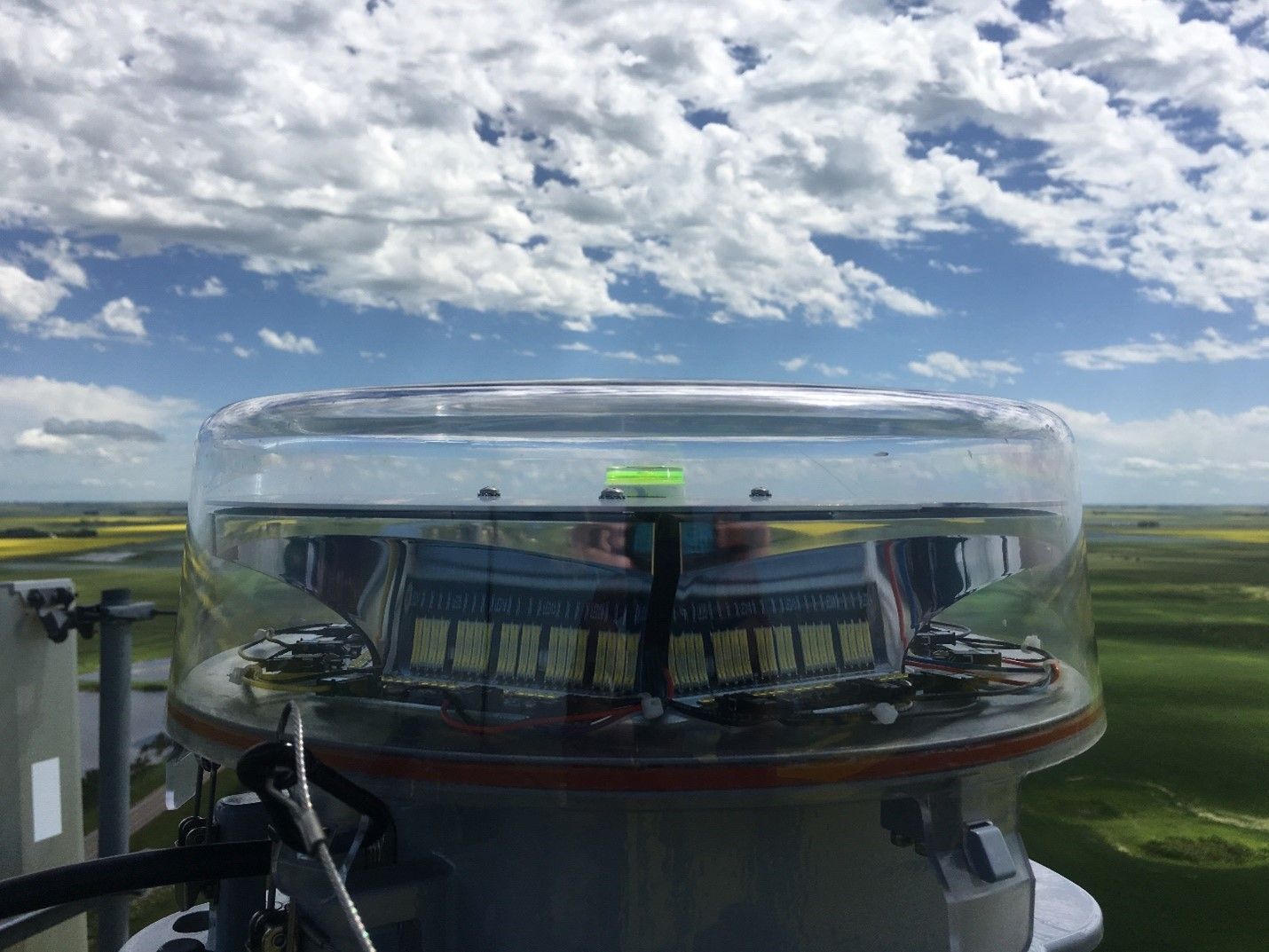
Simplify Your Tower Lighting Compliance with LumenServe℠ Attention tower owners! Staying on top of federally mandated lighting compliance regulations is crucial, but it doesn't have to be overwhelming. LumenServe℠ is here to help with our all-inclusive program that takes the stress out of compliance and monitoring. Are You Up to Date with FAA Regulations? Here's a straightforward compliance checklist: Monitor Your Lighting Systems: If there's an unresolved qualifying outage, file a Notice to Air Mission (NOTAM) with the FAA within 30 minutes, and clear the NOTAM once resolved. Daily Monitoring Logs: Create and maintain compliance logs for at least two years. Quarterly On-Site Inspections: Ensure your lighting systems are functioning correctly. Paint Inspections: Check the top portion of Style A towers. Biennial Lens Inspections: Regularly inspect your lenses every two years. Stay Ahead with New Regulations Regulations are always evolving. Whether it's the 7/8ths inch rule, IR lighting specifications, or the Avian standard, staying compliant can be a challenge. But that's where LumenServe℠ comes in! LumenServe℠ offers a complete range of compliance services to make your life easier: Compliance & Monitoring Services 24/7/365 Active Monitoring: Continuous monitoring of your lighting system. Remote Diagnostics: Quickly identify and resolve issues. FAA NOTAM Management: Reporting, tracking, and resolution. Daily Logs: Maintain logs with over two years of storage. Lighting Circular Validation FAA Rule Updates: Stay informed on new rules like the 7/8ths inch rule, IR LEDs, and aviation lighting regulations. Customer Reports: Stay in the loop with everything regarding your tower lighting. On-Site Tower Lighting Inspections Quarterly Lighting Inspections: Regular checks to ensure proper operation. Biennial Lens Inspections: Comprehensive lens checks every two years. Paint Inspections: For the top portion of Style A towers. Real-Time Monitoring and Updates With our 24/7/365 Network Operations Centers and customer portal, you'll always be informed about your tower’s health, alarm status, maintenance, and repair history. Trust LumenServe℠ for Compliance Rely on us to keep your tower compliant. Our expertise and scale can save you money and free up your time to focus on your core business. Contact LumenServe℠ today to learn more about our services. Contact Us Phone: (512) 580-4600 Email: info@LumenServe.com
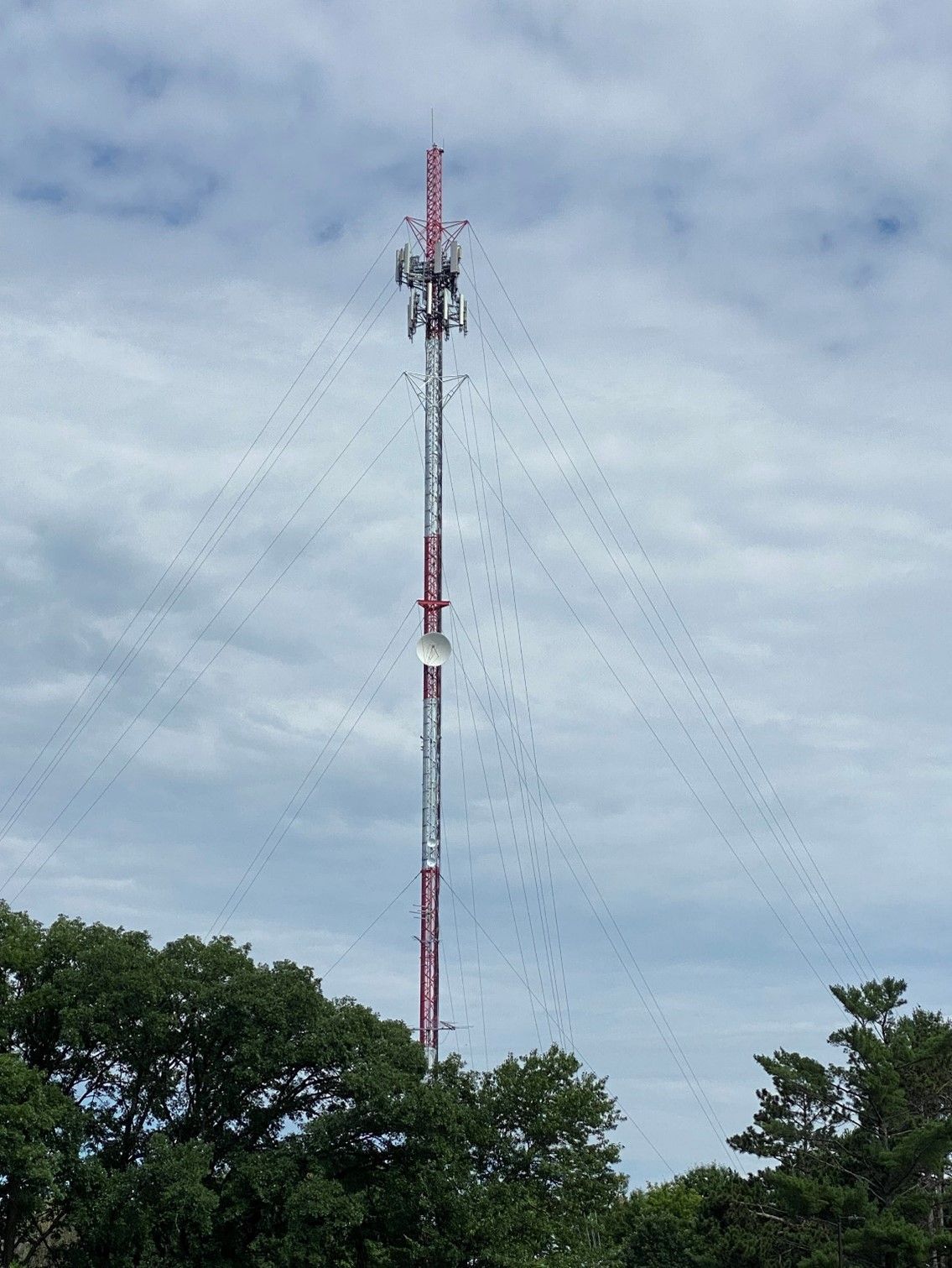
Tower owners with FAA Style A marking, which includes painted towers with red obstruction lighting at night, should be aware that there are cost-saving options to consider when it comes to periodic painting required for compliance. Here at LumenServe ℠ , our Never Paint Your Tower A gain program eliminates the need to repaint your tower for obstruction lighting purposes. First, let us clarify some background information. Painting of the structure: FAA Style A towers are painted to ensure visibility for air navigation, with specific requirements for painting the structure. The most important requirement is that the paint must meet the FAA's Aviation Orange color standard, which is Federal Standard 595 color #17875 for white and color #12197 for aviation orange. Additionally, the number of bands required on the tower depends on its height. You can visit our website for helpful information on each FAA Tower Style. Cost of painting of the structure: When evaluating the cost of painting a structure, there are five primary cost drivers: Material cost of paint – Paint costs approximately $70 per gallon with each gallon covering roughly 400 sq. ft. Tower type – There are three primary tower types - Guyed, Self-Supported, or Monopole. Each tower type is unique and requires a different amount of labor to complete depending on total surface area and other factors. Height of tower – As one would expect, the height of the tower is directly proportional to the amount of labor required to do the painting. Tower location – Tower crews charge to mobilize to the site. The more difficult it is to get to the location, the more the tower crew will charge to get there. Tower crew labor cost – The labor cost to paint your tower is typically based on the hours of work required for the project. Typically, labor will range from $25 per tower foot to $80 per tower foot depending on tower type, height, and location. Annual paint test:
In the world of tower maintenance, costs can soar to new heights, especially when it comes to climbs. Picture this: a typical climb on a 325’ tower can set you back a staggering $2,500 each time – a price that quickly accumulates with multiple climbs over the life of your lighting system. Now, what if we told you that there's a smarter, more cost-effective way to safeguard your tower's lighting without breaking the bank? Enter our fully comprehensive Assurance Warranty Service , an unbeatable solution that not only saves you money but offers peace of mind like never before. With an annual cost that is less than ½ of the cost a single tower climb referenced above, you'll receive not only all the tower climbs necessary to support your lighting system, but a level of support that covers everything from diagnostics to repairs, equipment replacements, mobilization and more. Our Assurance Warranty Service is only available with newly purchased and installed systems through LumenServe or through our Tower Lighting as a Service ® solution. Our Assurance Warranty Service is designed to be a game-changer in tower lighting maintenance. It covers the full array of services need to keep your system operational and in full compliance including: Problem diagnosis Remote troubleshooting Equipment replacement Site mobilization and expenses Repair labor on the ground Tower climb labor Shipping and transport RMA (Return Merchandise Authorization) Firmware upgrades All associated expenses In essence, it's your one-stop solution for ensuring the proper operation of your tower lighting system. Here are some more details on our Assurance Warranty Service . The math is simple: when you opt for the LumenServe℠ solutions that includes our Assurance Warranty, you're not just saving money; you're investing in long-term reliability and peace of mind. Say goodbye to the anxiety of unpredictable costs associated with tower climbs and embrace a more cost-effective and comprehensive approach to tower lighting maintenance. Join us on a journey where you can "Scale Heights, Not Costs," and let your tower shine brighter than ever before. For more information, please contact LumenServe℠ today!
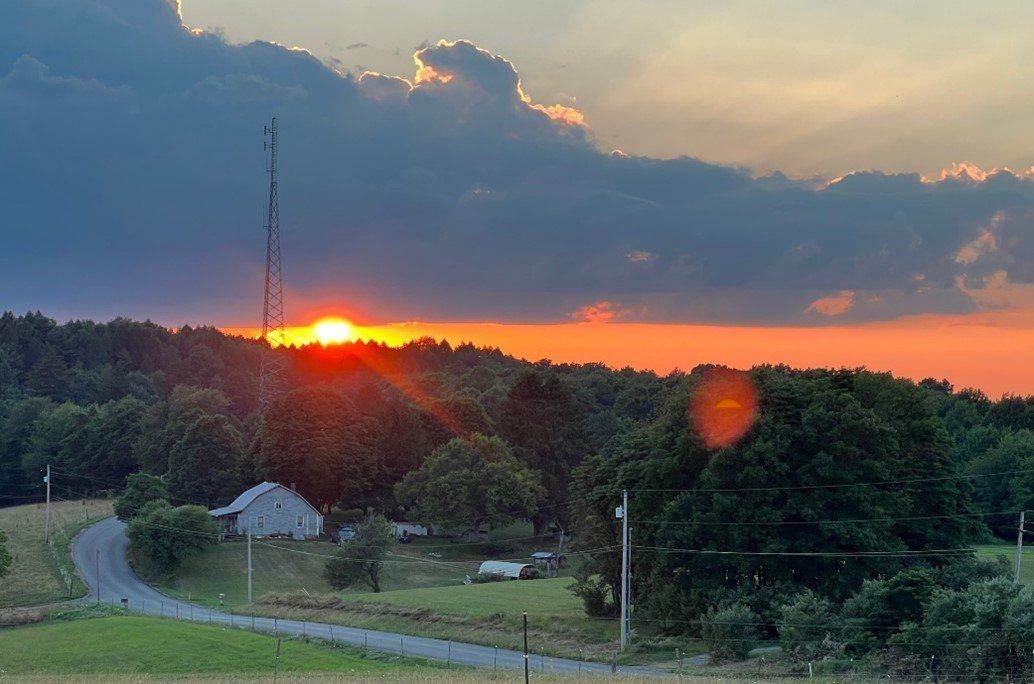
Virtually all lighting system original equipment manufacturers (OEMs) provide a warranty on their product, but what are you really getting with that warranty? With the Tower Lighting as a Service® approach from LumenServe℠ you get an Assurance Warranty that covers more than the average product warranty – we provide an end-to-end solution with no hidden costs. This ensures you stay on budget while not having to worry about your tower lighting. Let’s look at what you are getting (or not getting) with your current lighting system OEM warranty and compare it to what LumenServe offers in our bumper-to-bumper solution. The LumenServe℠ Assurance Warranty LumenServe℠ offers Assurance Warranty solutions as part of our full range of services that ensure that there are no unexpected costs with repairing and maintaining your system. Our approach is all inclusive: on ground, above ground, equipment and materials, labor and mobilization. You get flat pricing for up to five years so there are no budget surprises! How Does Your Current Lighting System Warranty Compare?
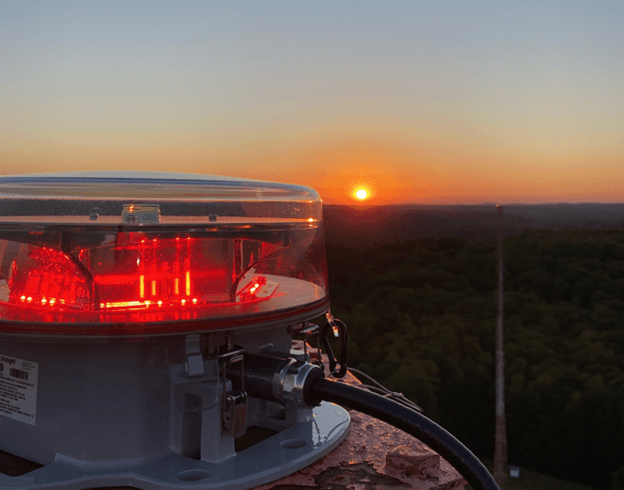
Let Us Help You Ensure FAA Compliance Keeping up with your towers’ federally mandated compliance and monitoring requirements is an expensive and time-consuming responsibility. Compliance is a must and requires you to constantly ensure that your towers adhere to the proper regulations with proper procedures and documentation. How would you like to never worry about this again… for zero upfront cost? LumenServe℠ is a full-service tower lighting company which means we take the burden of compliance and monitoring activities off your plate. Included with our unique Tower Lighting as a Service® program, is a full range of compliance services including: FAA Compliance & Reporting ● FAA NOTAM Reporting ● NOTAM Tracking and Resolution ● Lighting Circular Validation ● Notification of FAA Rule Updates such as: ○ 7/8 Inch Rule ○ IR LEDs ○ Aviation Lighting Regulations Monitoring ● Active Monitoring of Lighting ● 24/7/365 Monitoring ● Remote Diagnostics ● Daily Logs (2+ Years Storage) ● NOTAM Reporting to Customer ● Compliance Events On-site Tower Lighting Inspections ● Quarterly Lighting Inspections ● Biennial Lens Inspections ● Annual Paint Inspections at the top portion of the tower (Style A towers only) The new requirements related to Infrared Lighting (IR) are also an area we can help you with. Another option to learn more about is our Never Paint Your Tower Again where we assist you in changing your tower type from painted to dual mode. With Tower Lighting as a Service® . We will help you to update the FAA paperwork to make the change to dual mode, buy you a new lighting system, take care of it with our Assurance Warranty Service, and take care of the necessary compliance and monitoring. With our 24/7/365 Network Operations Centers and customer portal we can keep you informed of your tower’s overall system health status, alerts and alarm status maintenance and repair history. Your time is better spent on your core business and not on tower lighting. Let us use our size, scale, and expertise to free up your time to tend to your business and save you money too. To learn more about us and our services please contact LumenServe℠: (512) 580-4600 info@LumenServe.com